1 故障现象
近期投放市场的某挖掘机工作500h 后,客户反馈其动臂中加强板焊缝出现开裂故障,裂纹走向为中加强板与中侧板对接焊缝边缘,裂纹整齐、笔直,如图 1 所示。该客户还反馈出现裂纹后继续使用该动臂,裂纹未发生进一步扩展。
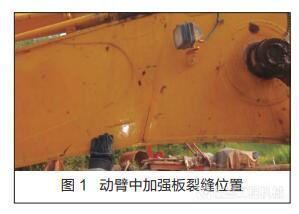
2 故障排查
2.1 产品调研
该型挖掘机动臂的对标产品为某日资和某国产的两款行业标杆品牌。挖掘机行业主要整机制造厂同吨位机型挖掘机均以该型日资品牌为对标机型,行业对该日资品牌产品的研究较为深入,产品质量得到市场的充分认可。根据市场调研获知,这两款行业标杆品牌的动臂市场表现极为优异,客户认可度较高。以上调研结果说明,该款动臂结构可满足质量要求。
2.2 有限元分析
选取动臂最大受力工况,对动臂开裂部位进行有限元分析,其应力云图如图 2 所示。从图 2 可知,应力分布自下而上逐渐变小,最大应力为 117MPa,远小于动臂 Q345C 材料 345MPa 许用应力。经计算,动臂安全系数为 2.9,远高于动臂 1.5 ~ 1.8 的理论安全系数,且动臂开裂部位最大应力区位于中加强板对接焊缝下半部,由此判断该动臂的
设计理论上满足要求。
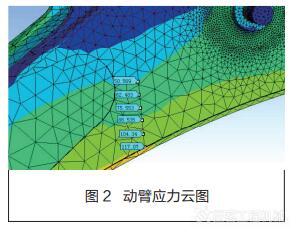
2.3 现场调查
为 排 查 故 障 原 因, 质 量、 技 术以及制作方共同参与了该机调查。从现 场 调 查 得 知, 该 故 障 动 臂 总 计 工作 2969.3h, 发 生 开 裂 时 间 为 工 作 到527.7h。现场检查发现该动臂共 2 处发生开裂,1 处位于动臂左侧中加强板焊缝下部(见图 1),另 1 处位于动臂右侧中加强板焊缝中部,如图 3 所示。
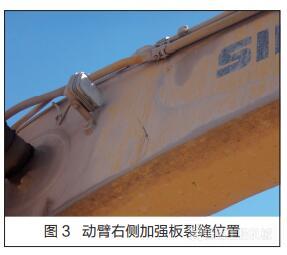
现场调查人员对裂缝的具体位置、深度以及中加强板拼装情况进行了详细的核查,初步确认两侧中加强板焊缝开裂,裂缝均发生于中加强板焊缝熔接处,裂缝深度为中加强板厚度,该动臂内部前侧板与中侧板的对接焊缝并未开裂。但是发现中加强板焊缝接近前侧板与中侧板的对接焊缝,未按图纸要求留出 5mm 焊接空间;中加强板与前侧板未完全贴合,实际拼装间隙为 1.2 ~2mm,如图 4 所示。
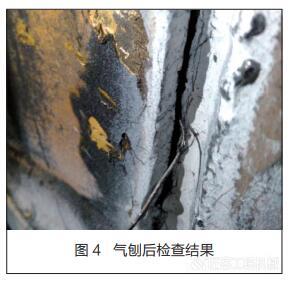
根据检查结果,初步判定故障原因有以下 2 点:一是焊缝与中加强板熔合不良;二是中加强板与前侧板拼装间隙过大,造成中加强板失去作用,导致中加强板焊缝因受力过大而开裂。
3 改进措施
根据故障原因,为加强该型挖掘机动臂中加强板焊接质量控制,现场调查人员提出了改进焊接工艺的 5 项具体要求:
一是严格控制中加强板与前侧板的贴合间隙,拼装前务必检查中加强板平整度是否满足
工艺要求,尽可能保证焊缝区域完全贴合,最大贴合间隙不得超过 0.5mm,否则该加强板将无任何加强作用,且极易开裂。
二是须先将前、中、后 3 块侧板完全拼焊后,再拼装中加强板,拼装中加强板的焊缝必须与前侧板和中侧板的对接焊缝错开 5mm,中加强板不得搭在焊缝上进行焊接,以保证焊缝与中加强板充分熔合,同时控制焊接缺陷。
三是焊接中加强板之前,须对中侧板附近的焊缝进行打磨处理,去除焊缝表面氧化皮、
飞溅等杂质。
四是焊接时采用合理的焊接工序,减小焊接变形对焊缝的不良影响,降低焊缝残余应力。
五是焊后须对中加强板焊缝进行严格的超声波质量检查,焊缝不符合要求必须气刨后重
新焊接,直至满足焊缝设计要求为止。
4 改进效果
严格执行改进措施后,该机型挖掘机动臂的焊缝质量及焊接可靠性得到大幅提升。截止
目前为止,按照改进后的工艺要求生产的该型挖掘机动臂无故障时间已达 7459h,客户的认可度极高,由此说明此次质量控制和工艺改进取得了显著效果。
作者:吴洋 孙中林 仇维蓉
来源:《工程机械与维修》2018年11期
修机 | 挖掘机动臂加强板焊缝开裂的原因 和改进措施
匠客工程机械 评论(0)
来源:匠客工程机械
1 故障现象
近期投放市场的某挖掘机工作500h 后,客户反馈其动臂中加强板焊缝出现开裂故障,裂纹走向为中加强板与中侧板对接焊缝边缘,裂纹整齐、笔直,如图 1 所示。该客户还反馈出现裂纹后继续使用该动臂,裂纹未发生进一步扩展。
2 故障排查
2.1 产品调研
该型挖掘机动臂的对标产品为某日资和某国产的两款行业标杆品牌。挖掘机行业主要整机制造厂同吨位机型挖掘机均以该型日资品牌为对标机型,行业对该日资品牌产品的研究较为深入,产品质量得到市场的充分认可。根据市场调研获知,这两款行业标杆品牌的动臂市场表现极为优异,客户认可度较高。以上调研结果说明,该款动臂结构可满足质量要求。
2.2 有限元分析
选取动臂最大受力工况,对动臂开裂部位进行有限元分析,其应力云图如图 2 所示。从图 2 可知,应力分布自下而上逐渐变小,最大应力为 117MPa,远小于动臂 Q345C 材料 345MPa 许用应力。经计算,动臂安全系数为 2.9,远高于动臂 1.5 ~ 1.8 的理论安全系数,且动臂开裂部位最大应力区位于中加强板对接焊缝下半部,由此判断该动臂的
设计理论上满足要求。
2.3 现场调查
为 排 查 故 障 原 因, 质 量、 技 术以及制作方共同参与了该机调查。从现 场 调 查 得 知, 该 故 障 动 臂 总 计 工作 2969.3h, 发 生 开 裂 时 间 为 工 作 到527.7h。现场检查发现该动臂共 2 处发生开裂,1 处位于动臂左侧中加强板焊缝下部(见图 1),另 1 处位于动臂右侧中加强板焊缝中部,如图 3 所示。
现场调查人员对裂缝的具体位置、深度以及中加强板拼装情况进行了详细的核查,初步确认两侧中加强板焊缝开裂,裂缝均发生于中加强板焊缝熔接处,裂缝深度为中加强板厚度,该动臂内部前侧板与中侧板的对接焊缝并未开裂。但是发现中加强板焊缝接近前侧板与中侧板的对接焊缝,未按图纸要求留出 5mm 焊接空间;中加强板与前侧板未完全贴合,实际拼装间隙为 1.2 ~2mm,如图 4 所示。
根据检查结果,初步判定故障原因有以下 2 点:一是焊缝与中加强板熔合不良;二是中加强板与前侧板拼装间隙过大,造成中加强板失去作用,导致中加强板焊缝因受力过大而开裂。
3 改进措施
根据故障原因,为加强该型挖掘机动臂中加强板焊接质量控制,现场调查人员提出了改进焊接工艺的 5 项具体要求:
一是严格控制中加强板与前侧板的贴合间隙,拼装前务必检查中加强板平整度是否满足
工艺要求,尽可能保证焊缝区域完全贴合,最大贴合间隙不得超过 0.5mm,否则该加强板将无任何加强作用,且极易开裂。
二是须先将前、中、后 3 块侧板完全拼焊后,再拼装中加强板,拼装中加强板的焊缝必须与前侧板和中侧板的对接焊缝错开 5mm,中加强板不得搭在焊缝上进行焊接,以保证焊缝与中加强板充分熔合,同时控制焊接缺陷。
三是焊接中加强板之前,须对中侧板附近的焊缝进行打磨处理,去除焊缝表面氧化皮、
飞溅等杂质。
四是焊接时采用合理的焊接工序,减小焊接变形对焊缝的不良影响,降低焊缝残余应力。
五是焊后须对中加强板焊缝进行严格的超声波质量检查,焊缝不符合要求必须气刨后重
新焊接,直至满足焊缝设计要求为止。
4 改进效果
严格执行改进措施后,该机型挖掘机动臂的焊缝质量及焊接可靠性得到大幅提升。截止
目前为止,按照改进后的工艺要求生产的该型挖掘机动臂无故障时间已达 7459h,客户的认可度极高,由此说明此次质量控制和工艺改进取得了显著效果。
作者:吴洋 孙中林 仇维蓉
来源:《工程机械与维修》2018年11期
敬请关注 《工程机械与维修》&《今日工程机械》 官方微信
更多精彩内容,请关注《工程机械与维修》与《今日工程机械》官方微信