2024年5月16日,2024工程机械行业科技节(以下简称科技节)在浙江杭州开幕。本届科技节以“高端·智能·绿色”为主题,立足新时代发展要求和国际视野,旨在通过创新形式,聚焦“产学研用”,激发工程机械行业科技创新的新动能和新优势,推动工程机械行业高质量发展。
5月17日,2024工程机械行业科技节十大科技创新进展发布仪式成功举办。
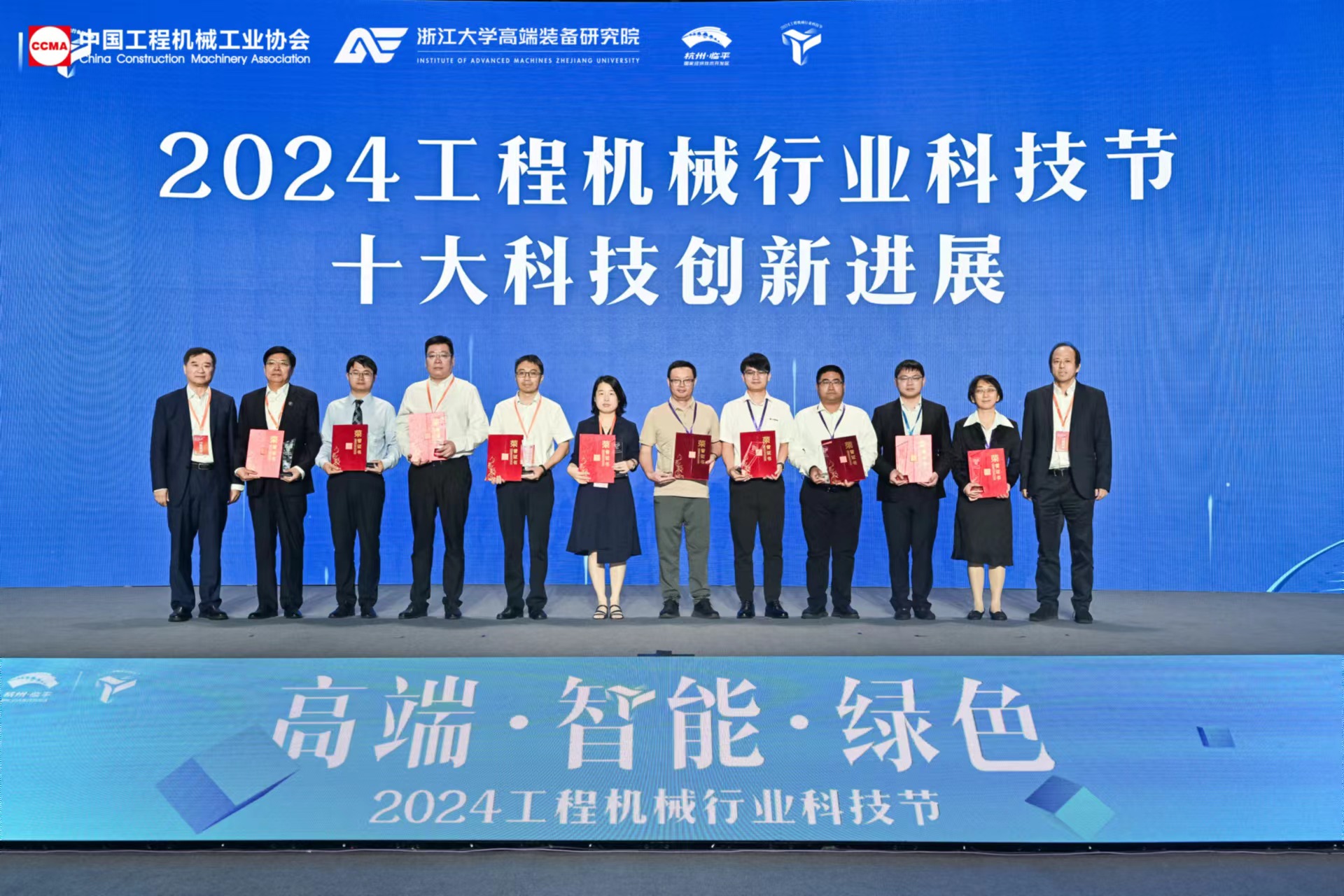
十大科技创新进展具体情况如下:
1、高机动轮式工程车辆悬挂关键技术创新及应用
主要完成单位:燕山大学,徐州重型机械有限公司,吉林大学
轮式工程车辆广泛应用于应急救援、工程矿山、交通运输、农林牧业、国防、航空航天笔领域,由于目前现有的轮式工程车辆采用常规悬挂,在非结构化复杂路面行驶的平顺性、操纵稳定性较差,越障能力不足,车轮载荷冲击大,影响了作业效率,业内要求改进的呼声较高。本成果在国家重点研发计划等多个项目支持下,对高机动主动悬挂技术、半主动悬挂技术、被动悬挂技术和主/被动悬挂切换技术进行了系统创新。
(1)提出了主动悬挂的惯性调控原理和基本控制方法。解决了车辆设计领域一直存在的“行驶平顺性和操纵稳定性相互制约、难以同步提高”的世界性难题。所研发的主动悬挂,不需要分工况控制,与油气悬挂相比:①行驶平顺性显著提高;②操纵稳定性阶跃式提升;③越障能力和触地性能有了革命性的进步;④不平地面行驶的最大轮荷和轮荷波动幅值显著下降。
(2)发明了一种刚度、阻尼和行程可调的油气半主动悬挂控制技术。解决具有多轴荷状态的轮式工程车辆一直存在的小轴荷侧倾俯仰大、大轴荷行驶冲击大的难题,可分工况自适应调整悬挂系统的刚度和阻尼。
(3)发明了大承载双横臂独立悬挂机构。解决现有双横臂独立悬挂载重受限难题,将弹性元件承载的车重通过转向节直接传递至轮胎,最大限度地增加了弹性阻尼元件的杠杆比。
(4)发明了主/被动悬挂快速切换控制系统。通过在主/被动悬挂双向切换之前,调平车身并控制各悬挂油缸行程平均值处于油缸行程中位值,有效消除了切换时车体的振颤。
本项目共获得专利授权67项,其中中国发明专利35项,国际PCT专利32项;发表论文24篇,其中SCI检索17篇,EI检索7篇。项目成果已在徐工集团系列全地面起重机和消防车上得到了推广应用,其中全地面起重机在世界上首次斜对角车轮同时越过了400mm 高的梯形障碍;云梯高喷消防车在世界上首次实现不平路面的行进举高灭火功能。2019至2023年间累计实现新增销售37.16亿、利润3.22亿、税收0.95亿。经鉴定,项目整体技术达到国际先进水平,其中高机动主动悬挂、被动悬挂和主/被动悬挂切换技术达到国际领先水平。
2、ZAT24000H全地面起重机关键技术及产品应用
主要完成单位:中联重科股份有限公司
行业首创、全球最大吨位ZAT24000H全地面起重机,是中联重科为新能源建设打造的施工利器。该产品突破自我极限,再次刷新全球最大吨位全地面起重机纪录。
产品为风电领域量身打造,100米高度风机最大吊重270吨,其最大起升高度175米吊重175吨,相当于一次起吊117台小汽车到60层楼高度,在超高重载集约型全地面起重机整机设计技术、超长重载复杂臂架系统设计制造技术、长柔大惯量臂架精准安全作业控制技术、超重载多轴底盘自适应行驶控制技术等方面,实现了数十项原创技术突破,整体技术及产品指标达到国际领先水平。
2022年6月以来,在国内140米高度单机发电量最大的集中式批量混塔风场-黑河赵光风电项目、云南昆明巨龙梁风电项目、张家口沽源十里山风电项目、广西合浦西乌风电项目等大型风电项目中投入使用,用户评价“产品性能强大、施工效率高、转场运输上具有无可替代的优势。先进的控制系统和微动操控性能为施工安全提供了有力保障,施工效益显著”。该全地面起重机作为风机吊装的核心装备,将持续在全国各大风电施工项目建设中发挥重要作用。
3、级间双反馈型大流量平衡阀
主要完成单位:浙江大学高端装备研究院、浙江大学
(1)针对大流量平衡阀先导多级控制问题,本项目原创性提出了一种级间液压-机械双反馈阀芯控制新原理、阀芯动态测试方法,具有较高频响与反馈控制力大的优点,同时通过双反馈链路交叉耦合设计方式提高了阀芯动力学稳定性,有效解决了大流量平衡阀在大流量动态稳定性、启闭时滞特性以及防失速等方面的国际性难题。级间液压-机械双反馈的阀芯控制新原理,其中液压反馈通过反馈阀口的设计,实现主阀芯位移-先导流量-敏感腔压力的反馈,机械反馈则通过反馈弹簧实现双阀芯的快速线性位移-力反馈原理。该原理具有频响快、反馈控制力强的性能优势,同时可实现阀芯对置分布,具有结构紧凑、配合面少的优点大幅降低制造难度。
(2)为使大流量平衡阀具有较好的微调特性,精确控制主阀口流量,本项目提出了先导阀口的分段补偿原理。设计了带预补偿阀口的先导分段补偿结构,解决了缺少必要的微调控制区间、小开口下的流量分辨率较低、微调通流面积过小造成的流量死区过大的难题,有效降低了先导开启压力,改善了微调控制区间,并提高了平衡阀的比例控制性能。
(3)针对高背压下易失速、控制区间变化的问题,本针对高背压下易失速、控制区间变化的问题,本项目提出了先导回油背压补偿原理,将背压增量通过先导回油口、先导阀口阻尼、过补偿阻尼反馈至主阀芯大端作用腔,限制高背压下主阀口流量增大,采用先导回油背压反馈方案可达到背压升高主阀口流量略有降低的效果,提高了平衡阀的防失速性能,并且先导控制压力区间保持不变,保证了背压变化时的操控性能。
(4)双反馈原理平衡阀的主阀芯属于内流式锥阀形式,所受液动力作用方向将使阀口趋于打开,大流量下液动力幅值常达阀芯驱动力30%以上,严重影响阀芯动态控制性能,并带来阀芯失控的隐患。本项目提出基于带通油孔的减振尾结构的非全周开口大流量锥滑阀芯反向液动力补偿方法,该结构可通过液流冲击作用抵消开启方向的液动力,进而改变阀芯液动力的方向,同时降低各阀口开度下的液动力幅值,增加了主阀芯的稳定性并基本消除了液动力对主阀芯位移控制精度的影响。
4、高空大吊载轮式起重装备自主研发与产业化
主要完成单位:徐州重型机械有限公司,徐工集团工程机械股份有限公司建设机械分公司
高端工程装备研制能力体现了一个国家的综合制造实力,大型起重装备因必须同时满足吊载高度和吊载重量的需求,是工程机械中难度最大、技术最复杂的重点装备之一。项目实施前,核心技术长期被德国和美国垄断,严重制约我国重大工程施工建设。
另外,随着我国风电产业持续发展,在“十四五”可再生能源发展规划中,确定了2025年风电实现翻倍的目标。同时风机持续大型化发展,安装高度达到160m、重量达到146吨。项目前,我国起重机产品难以满足风电大型化发展需求。
本项目立足突破起重机性能极限,并结合我国“双碳”战略发展需求,针对风电吊装装备能力不足的行业难题,系统性地攻克了高空大吊载起重机臂架结构技术、高空吊载主动安全技术、重型起重机高效转场技术、起重机高空吊载自牵引揽风绳系统,全面掌握轮式起重机、履带式起重机核心关键技术,研制出吊载能力最强的轮式起重机、风电安装效率最高的履带式起重机,实现了对国际标杆从跟跑、并跑到领跑的跨越。
项目获中国授权发明专利43件、欧美等国际专利13件、软件著作权4件,制修订国家标准6项,主持起草中国起重机行业首个国际标准。项目产品性能及关键技术水平,经第三方检测和中国机械工业联合会鉴定,国际领先。
项目成果应用产品经济效益超90亿元,因降低施工场地基建成本、缩短施工周期产生的间接经济效益超230亿元。产品应用于全球陆上最大风电项目酒泉600万千瓦风电场、国产航母建设等重大工程,项目产品被评为“建国70周年工程机械行业杰出产品”,获“中国工业大奖”。项目成果促进了我国起重装备的自主创新能力和技术进步,公司连续两年位居“全球起重机制造商”“全球移动式起重机制造商”排行榜双榜首。
5、智能型凿岩台车关键技术研究及应用
主要完成单位:中国铁建重工集团股份有限公司
我国已建成和在建的隧道数量和长度均居世界第一,且隧道的分布广度、地质复杂程摩修建难度居世界之最。目前隧道建设70%以上采用钻爆法施工,但传统人工钻爆法隧道修建方法将难以满足国家基础设施高质量快速发展的需要。项目实施前,人工钻爆法隧道施工普通采用人工风钻方式,人员需求多、劳动强度高、施工效率低、施工安全无保障。即使少数采用游压凿岩台车,仍存在地质风险高、施工精度低、质量控制差等难题,且设备长期依赖进口。
随着郑万高铁、川藏铁路等为代表的国家重点工程发展需求,急需研制一系列国产化高隧道智能装备。基于此,本项目集合优势力量进行长期科研攻关,成功突破了智能型凿岩装备围岩智能分级、精准钻进控制、三维扫描重建等关键核心技术,研制出具有数字化控制、多重感知、自主分析决策能力的智能型凿岩台车并实现产业化,对推动我国隧道工程高质量发展、加快实现隧道智能建造具有重要意义。
由湖南省机械工业协会组织的丁荣军院士任组长的鉴定专家组一致认为:该项目技术难度大,创新性强,总体技术达到国际领先水平。本项目提升智能型凿岩台车关键核心部件制造过程的数字化、智能化水平,实现人均产出效率提升50%以上。项目还形成了适应于不同领域不同工况的凿岩台车系列化产品,带动了产业链整体发展。项目成果已在郑万高铁、玉铁路等重点工程以及国防建设中成功应用,推动了我国从隧道建设大国向隧道建设强国的转变。
6、面向数字化工程机械的数字液压泵关键技术及应用
主要完成单位:浙江大学、苏州力源液压有限公司
项目针对重载大流量数字泵的关键技术及应用展开研究,在国家04科技重大专项、国家科技支撑计划、工信部战略基础产品等项目支持下,历经十余年的产学研持续攻关,取得了如下创新发明成果:
(1)针对柱塞泵四象限变量过程油膜承载动态交变大、宽工作区间效率低的难题,建立摩擦副壁面的弹性变形与油液可压缩性缝隙流动下的液固气三相耦合的油膜模型,对摩擦副表面结构进行了优化设计,提升了产品可靠性,研发了系列化四象限高压大排量数字泵。
(2)针对大型装备压力高、流量大、负载多、载荷波动,提出了数字泵可编程控制方法,攻克了变量机构高动态控制和复杂系统流量精准匹配技术,研发了数字泵可编程控制系统,实现了液压泵工作模式和控制参数自适应切换(变量响应<250ms)。
(3)针对复杂工况下数字泵的服役退化评估难、故障辨识准确率低的行业难题,提出了高斯遗传向量回归诊断模型,实现了变工况状态特征的实时提取和精准辨识,在线模型重训练时间2.55s,典型故障诊断准确率99.72%。
(4)研制了系列化可编程数字泵产品,攻克了重载大排量可编程数字泵设计制造关键技术装机应用于盾构掘进机、混凝土泵车、挖掘机、起重机等工程装备,实现国产化替代。
7、第一代新能源电驱动装载机研制及产业化应用
主要完成单位:广西柳工机械股份有限公司、柳工柳州传动件有限公司、广西中源机械有限公司、重庆大学
本项目突破传统的柴油机加双变(变矩器变速箱)系统的动力传动链结构的装载机边界创新性的使用电动机作为牵引装置,应用动力电池组作为动力能源,在达到零排放的同时,现或超越同级别传统装载机整机性能的新能源电驱动装载机。
突破传统的整机匹配技术,研究电驱动整机匹配技术。突破大电量高压储能及电能分配技术,研究大电量高压储能电池管理系统BMS,研究制动能量回收技术、节能液压技术。研究基于主动工况需求识别的动态功率分配控制系统。研究均流系统中多电机设备电流自适应分配控制技术,开发行走电机及液压电机控制策略。研究基于环境识别的能效自适应管理技术。突破高效节能新型驱动技术,研究电驱动动力传动技术,建立传动系统工作模型,开发电驱专用速箱。研究突破整机热管理技术,特别是锂电池热管理安全技术。建立声品质测试与评价方法通过声品质与主动降噪技术的融合,达到NH特性的提升。研究电驱动智能遥控技术,研究基于不同工况物料的自适应铲装技术。
在上述技术获得突破后开发柳工1.6T、2T、5T级系列新能源电驱动装载机。重点突破国内电驱动装载机的产业化空白,实现批量销售,开拓工程机械电驱动产业化的新领域。
本项目同时针对高原遂道工况突破高原适应性研究,以填补国家在该领域产品空白,积极响应政府号召,满足川藏铁路施工段隧道特殊工况的迫切需求。
目前拥有自主知识产权专利共52项,其中发明专利29项。获得省部级与行业级奖项共7项。近年来,公司在电控技术、负载敏感技术方面的技术攻关取得较大突破,连续两年获得广西科学技术奖二等奖:2018年公司新产品开发项目《装载机转向高压负荷敏感流量放大阀关键技术与应用》获得广西科学技术奖技术发明类二等奖,2019年公司研发项目《起重机负载敏感多路阀开发及其上车液压系统匹配应用》获得广西科学技术奖技术发明类二等奖。
8、高压大排量柱塞泵关键技术研究及产业化
主要完成单位:江苏恒立液压股份有限公司
高压大排量桂塞泵由配流盘、滑靴等组成,具备抗污能力强、噪声低、多种控制方式控制等特点,实现对国外同等产品之间的替代,打造国产高压大排量柱泵。本项目针对高压大排量柱塞泵的额定压力、噪声处理、控制方式等问题开展了相关关键技术研究:
(1)设计了新的双泵支承结构,大幅度缩短主轴向尺寸,有效节省了安装空间,提高泵的使用寿命和抗污染能力。
(2)采用了配流盘过渡区通孔和盲孔结合的形式,避免了轴向柱塞泵气穴、气蚀,降低柱塞腔压力突变,并通过对配流盘开设阻尼孔和指形槽相结合的方式,提高了配流盘的抗气蚀能力,并且采用该种配流盘可以有效降低整泵的噪声,使柱塞泵噪声<85dB。
(3)设计了电比例排量闭环控制器,通过斜盘角度传感器,实现了泵输出流量的闭环精确控制,提升了效率,降低了能耗,并根据控制方式设计相应控制器,使液压泵具有集成流量控制功率控制、压力控制、电比例闭环控制等变量控制方式。
本项目紧紧围绕我国工程机械的客观需求,充分发挥恒立液压作为中国高端液压泵阀行业的龙头企业的优势,以实现高压大排量柱塞泵国产化为目标,提升核心液压件的研发能力和技术水平,解决核心零部件主要依赖进口的局面。本项目成果整体技术指标达到国际同类产品水平,处于国内领先。产品已在三一、徐工、柳工等厂家的旋挖钻机上批量配套,实现对国外产品的进口替代。近三年实现了5852套产品销售,销售收入14821万元,新增利税5324万元。
9、千吨级履带起重机关键技术及应用
主要完成单位:浙江三一装备有限公司,湖州师范学院
我国大吨位履带起重机长期存在系统分析精度低、侧向承载稳定性差、机构协同控制效案低等技术瓶颈,无法满足大型核电、石化、风电场等工程场景的施工需求。本项目在国家86计划支持下,经9年持续攻关,在集成系统设计、机构协同、臂架结构三大方向取得了关键性进展,形成了千吨级履带起重机系列产品,成功实现国产化替代。项目获发明专利9件、软著3 件、发表论文6篇、参与国标1项、牵头制定团标1项。主要技术内容如下:
(1)基于大型履带起重机整体仿真设计:自主集成开发了千吨级履带起重机总体设计软件设计电子载荷表计算系统、臂架专用仿真程序、履带板自动缠绕建模仿真系统及数字孪生仿真系统,解决臂架系统非线性精确分析及超级回转装置回转支承和环轨力的精确计算问题,精度>94%,开发国内唯一接地比压实时监控、评估系统,高效评估地基承载能力,实现空载接地比压0.24MPa,较竞品提升22.5%,提高本项目整体系统的分析精度,分析精度>95%,避免核电、石化等重大工程的安全事故。
(2)基于大型履带起重机高稳定性关键结构设计:首创的高强度高刚度臂架系统可根据需要高效组合成预设宽度的变径平行臂架,侧向承载稳定性提升2.5倍,最大额定起重量突破4500吨;国内首创内回转支承加外环轨的超级回转支承系统,避免在内外部安装检测装置时机械产生滑动产生误差累计,回转速度为0.024rpm,较国际同类产品提升96%。
(3)基于大型履带起重机多机构协同控制系统设计:首次开发了多动力多机构系统协同控制技术,国际先进的双发驱动闭式液压系统,避免吊钩无法自由落钩:国内首创的千吨级起重机智能控制系统,通过力矩限制器免空钩标定算法,解决双驱行走、多卷扬、双发动机协同、超起小车与主机同步回转与行走、多卷扬穿绳效率的问题,防止系统失控导致钢丝绳损坏的问题实现变幅卷扬绳速110m/min,较同类产品提升10m/min。
项目成功应用在核电、石化等关系国计民生的重点工程中,如:CAP1400国核示范、山东鲁清石化、印度Gujarat风电场等项目,近五年新增产值74.3亿,新增利税24.4亿,创收外汇15.6亿。项目获得“明星产品、国之重器奖”、中国工程机械TOP50“技术创新金奖”、浙江省首台套等荣誉,在中国人民政府网、人民日报等各大媒体中被誉为“全球第一吊”。经浙江省工业新产品验收组鉴定,本项目己达到国际先进水平。
10、高速高压气动液压核心基础零部件关键技术及应用
主要完成单位:同济大学、上海振中建机科技有限公司、浙江永安工程机械有限公司
高速、高精度、超高压气动液压技术源于航空航天、用于工程机械、氢能源汽车及重大装备。核心基础零部件(元器件)是国家“制造强国战略”“工业强基”的重点突破瓶颈之一。气体非线性、气体压缩与释放过程的非对称性、超高压气体分子间作用力等是世界性的基础难题。在国家科技计划和国家自然科学基金等连续资助下,经过近二十年潜心研究和原始创新,在高速高精度气动液压控制方法与元件、重大装备瓶颈技术方面取得突破性进展。主要技术发明为:
(1)针对多年来困扰气动系统的低速和非线性问题,发明了高速高精度气动控制方法,进步发明了一种带套管钻的大直径气动潜孔锤,首次提出并实现了双通道潜孔锤,所研制的双通道回转接头可同时注浆注气,形成了螺旋排渣贯通式大直径气动潜孔锤设计方法。
(2)针对超高压气动控制阀及其系统的国际性难题,提出了70MPa和35MPa超高压分级压力控制方法,发明了高压气动减压阀、动静态补偿与非对称控制方法,自主研发了达到和超过国外同类产品水平的先进适用的车载超高压控制阀,实现极端低温(-40℃)和极端高温(+60℃)下输氢、加氢过程的快速充放以及行驶过程的超高压稳定控制。
(3)发明了利用加速度技术的气动液压复合打桩锤系统,通过压缩气体和锤体惯性质量的综合作用,实现锤体加速度2g以上的高速打桩。发明了可调偏心振动锤、新型气液联动复合液压缸、水下打桩用大型分体式替打,提出了基于氮气及蓄能器的打击能量调节方法。
该系列成果获授权发明专利48项,编制国家标准2项、行业标准4项,出版中文专著1部、英文专著1部,获优秀科技图书一等奖。发明成果气动潜孔锤应用于复杂地层桩基施工。发明成果超高压气动控制阀用于氢能源汽车示范应用。发明成果气动液压锤用于深海风电基础平台等国家重大工程任务。近五年累计产值16.82亿元。项目成果社会、经济效益显著。
工程机械行业科技节十大科技创新进展正式发布
匠客工程机械 评论(0)
来源:匠客工程机械
2024年5月16日,2024工程机械行业科技节(以下简称科技节)在浙江杭州开幕。本届科技节以“高端·智能·绿色”为主题,立足新时代发展要求和国际视野,旨在通过创新形式,聚焦“产学研用”,激发工程机械行业科技创新的新动能和新优势,推动工程机械行业高质量发展。
5月17日,2024工程机械行业科技节十大科技创新进展发布仪式成功举办。
十大科技创新进展具体情况如下:
1、高机动轮式工程车辆悬挂关键技术创新及应用
主要完成单位:燕山大学,徐州重型机械有限公司,吉林大学
轮式工程车辆广泛应用于应急救援、工程矿山、交通运输、农林牧业、国防、航空航天笔领域,由于目前现有的轮式工程车辆采用常规悬挂,在非结构化复杂路面行驶的平顺性、操纵稳定性较差,越障能力不足,车轮载荷冲击大,影响了作业效率,业内要求改进的呼声较高。本成果在国家重点研发计划等多个项目支持下,对高机动主动悬挂技术、半主动悬挂技术、被动悬挂技术和主/被动悬挂切换技术进行了系统创新。
(1)提出了主动悬挂的惯性调控原理和基本控制方法。解决了车辆设计领域一直存在的“行驶平顺性和操纵稳定性相互制约、难以同步提高”的世界性难题。所研发的主动悬挂,不需要分工况控制,与油气悬挂相比:①行驶平顺性显著提高;②操纵稳定性阶跃式提升;③越障能力和触地性能有了革命性的进步;④不平地面行驶的最大轮荷和轮荷波动幅值显著下降。
(2)发明了一种刚度、阻尼和行程可调的油气半主动悬挂控制技术。解决具有多轴荷状态的轮式工程车辆一直存在的小轴荷侧倾俯仰大、大轴荷行驶冲击大的难题,可分工况自适应调整悬挂系统的刚度和阻尼。
(3)发明了大承载双横臂独立悬挂机构。解决现有双横臂独立悬挂载重受限难题,将弹性元件承载的车重通过转向节直接传递至轮胎,最大限度地增加了弹性阻尼元件的杠杆比。
(4)发明了主/被动悬挂快速切换控制系统。通过在主/被动悬挂双向切换之前,调平车身并控制各悬挂油缸行程平均值处于油缸行程中位值,有效消除了切换时车体的振颤。
本项目共获得专利授权67项,其中中国发明专利35项,国际PCT专利32项;发表论文24篇,其中SCI检索17篇,EI检索7篇。项目成果已在徐工集团系列全地面起重机和消防车上得到了推广应用,其中全地面起重机在世界上首次斜对角车轮同时越过了400mm 高的梯形障碍;云梯高喷消防车在世界上首次实现不平路面的行进举高灭火功能。2019至2023年间累计实现新增销售37.16亿、利润3.22亿、税收0.95亿。经鉴定,项目整体技术达到国际先进水平,其中高机动主动悬挂、被动悬挂和主/被动悬挂切换技术达到国际领先水平。
2、ZAT24000H全地面起重机关键技术及产品应用
主要完成单位:中联重科股份有限公司
行业首创、全球最大吨位ZAT24000H全地面起重机,是中联重科为新能源建设打造的施工利器。该产品突破自我极限,再次刷新全球最大吨位全地面起重机纪录。
产品为风电领域量身打造,100米高度风机最大吊重270吨,其最大起升高度175米吊重175吨,相当于一次起吊117台小汽车到60层楼高度,在超高重载集约型全地面起重机整机设计技术、超长重载复杂臂架系统设计制造技术、长柔大惯量臂架精准安全作业控制技术、超重载多轴底盘自适应行驶控制技术等方面,实现了数十项原创技术突破,整体技术及产品指标达到国际领先水平。
2022年6月以来,在国内140米高度单机发电量最大的集中式批量混塔风场-黑河赵光风电项目、云南昆明巨龙梁风电项目、张家口沽源十里山风电项目、广西合浦西乌风电项目等大型风电项目中投入使用,用户评价“产品性能强大、施工效率高、转场运输上具有无可替代的优势。先进的控制系统和微动操控性能为施工安全提供了有力保障,施工效益显著”。该全地面起重机作为风机吊装的核心装备,将持续在全国各大风电施工项目建设中发挥重要作用。
3、级间双反馈型大流量平衡阀
主要完成单位:浙江大学高端装备研究院、浙江大学
(1)针对大流量平衡阀先导多级控制问题,本项目原创性提出了一种级间液压-机械双反馈阀芯控制新原理、阀芯动态测试方法,具有较高频响与反馈控制力大的优点,同时通过双反馈链路交叉耦合设计方式提高了阀芯动力学稳定性,有效解决了大流量平衡阀在大流量动态稳定性、启闭时滞特性以及防失速等方面的国际性难题。级间液压-机械双反馈的阀芯控制新原理,其中液压反馈通过反馈阀口的设计,实现主阀芯位移-先导流量-敏感腔压力的反馈,机械反馈则通过反馈弹簧实现双阀芯的快速线性位移-力反馈原理。该原理具有频响快、反馈控制力强的性能优势,同时可实现阀芯对置分布,具有结构紧凑、配合面少的优点大幅降低制造难度。
(2)为使大流量平衡阀具有较好的微调特性,精确控制主阀口流量,本项目提出了先导阀口的分段补偿原理。设计了带预补偿阀口的先导分段补偿结构,解决了缺少必要的微调控制区间、小开口下的流量分辨率较低、微调通流面积过小造成的流量死区过大的难题,有效降低了先导开启压力,改善了微调控制区间,并提高了平衡阀的比例控制性能。
(3)针对高背压下易失速、控制区间变化的问题,本针对高背压下易失速、控制区间变化的问题,本项目提出了先导回油背压补偿原理,将背压增量通过先导回油口、先导阀口阻尼、过补偿阻尼反馈至主阀芯大端作用腔,限制高背压下主阀口流量增大,采用先导回油背压反馈方案可达到背压升高主阀口流量略有降低的效果,提高了平衡阀的防失速性能,并且先导控制压力区间保持不变,保证了背压变化时的操控性能。
(4)双反馈原理平衡阀的主阀芯属于内流式锥阀形式,所受液动力作用方向将使阀口趋于打开,大流量下液动力幅值常达阀芯驱动力30%以上,严重影响阀芯动态控制性能,并带来阀芯失控的隐患。本项目提出基于带通油孔的减振尾结构的非全周开口大流量锥滑阀芯反向液动力补偿方法,该结构可通过液流冲击作用抵消开启方向的液动力,进而改变阀芯液动力的方向,同时降低各阀口开度下的液动力幅值,增加了主阀芯的稳定性并基本消除了液动力对主阀芯位移控制精度的影响。
4、高空大吊载轮式起重装备自主研发与产业化
主要完成单位:徐州重型机械有限公司,徐工集团工程机械股份有限公司建设机械分公司
高端工程装备研制能力体现了一个国家的综合制造实力,大型起重装备因必须同时满足吊载高度和吊载重量的需求,是工程机械中难度最大、技术最复杂的重点装备之一。项目实施前,核心技术长期被德国和美国垄断,严重制约我国重大工程施工建设。
另外,随着我国风电产业持续发展,在“十四五”可再生能源发展规划中,确定了2025年风电实现翻倍的目标。同时风机持续大型化发展,安装高度达到160m、重量达到146吨。项目前,我国起重机产品难以满足风电大型化发展需求。
本项目立足突破起重机性能极限,并结合我国“双碳”战略发展需求,针对风电吊装装备能力不足的行业难题,系统性地攻克了高空大吊载起重机臂架结构技术、高空吊载主动安全技术、重型起重机高效转场技术、起重机高空吊载自牵引揽风绳系统,全面掌握轮式起重机、履带式起重机核心关键技术,研制出吊载能力最强的轮式起重机、风电安装效率最高的履带式起重机,实现了对国际标杆从跟跑、并跑到领跑的跨越。
项目获中国授权发明专利43件、欧美等国际专利13件、软件著作权4件,制修订国家标准6项,主持起草中国起重机行业首个国际标准。项目产品性能及关键技术水平,经第三方检测和中国机械工业联合会鉴定,国际领先。
项目成果应用产品经济效益超90亿元,因降低施工场地基建成本、缩短施工周期产生的间接经济效益超230亿元。产品应用于全球陆上最大风电项目酒泉600万千瓦风电场、国产航母建设等重大工程,项目产品被评为“建国70周年工程机械行业杰出产品”,获“中国工业大奖”。项目成果促进了我国起重装备的自主创新能力和技术进步,公司连续两年位居“全球起重机制造商”“全球移动式起重机制造商”排行榜双榜首。
5、智能型凿岩台车关键技术研究及应用
主要完成单位:中国铁建重工集团股份有限公司
我国已建成和在建的隧道数量和长度均居世界第一,且隧道的分布广度、地质复杂程摩修建难度居世界之最。目前隧道建设70%以上采用钻爆法施工,但传统人工钻爆法隧道修建方法将难以满足国家基础设施高质量快速发展的需要。项目实施前,人工钻爆法隧道施工普通采用人工风钻方式,人员需求多、劳动强度高、施工效率低、施工安全无保障。即使少数采用游压凿岩台车,仍存在地质风险高、施工精度低、质量控制差等难题,且设备长期依赖进口。
随着郑万高铁、川藏铁路等为代表的国家重点工程发展需求,急需研制一系列国产化高隧道智能装备。基于此,本项目集合优势力量进行长期科研攻关,成功突破了智能型凿岩装备围岩智能分级、精准钻进控制、三维扫描重建等关键核心技术,研制出具有数字化控制、多重感知、自主分析决策能力的智能型凿岩台车并实现产业化,对推动我国隧道工程高质量发展、加快实现隧道智能建造具有重要意义。
由湖南省机械工业协会组织的丁荣军院士任组长的鉴定专家组一致认为:该项目技术难度大,创新性强,总体技术达到国际领先水平。本项目提升智能型凿岩台车关键核心部件制造过程的数字化、智能化水平,实现人均产出效率提升50%以上。项目还形成了适应于不同领域不同工况的凿岩台车系列化产品,带动了产业链整体发展。项目成果已在郑万高铁、玉铁路等重点工程以及国防建设中成功应用,推动了我国从隧道建设大国向隧道建设强国的转变。
6、面向数字化工程机械的数字液压泵关键技术及应用
主要完成单位:浙江大学、苏州力源液压有限公司
项目针对重载大流量数字泵的关键技术及应用展开研究,在国家04科技重大专项、国家科技支撑计划、工信部战略基础产品等项目支持下,历经十余年的产学研持续攻关,取得了如下创新发明成果:
(1)针对柱塞泵四象限变量过程油膜承载动态交变大、宽工作区间效率低的难题,建立摩擦副壁面的弹性变形与油液可压缩性缝隙流动下的液固气三相耦合的油膜模型,对摩擦副表面结构进行了优化设计,提升了产品可靠性,研发了系列化四象限高压大排量数字泵。
(2)针对大型装备压力高、流量大、负载多、载荷波动,提出了数字泵可编程控制方法,攻克了变量机构高动态控制和复杂系统流量精准匹配技术,研发了数字泵可编程控制系统,实现了液压泵工作模式和控制参数自适应切换(变量响应<250ms)。
(3)针对复杂工况下数字泵的服役退化评估难、故障辨识准确率低的行业难题,提出了高斯遗传向量回归诊断模型,实现了变工况状态特征的实时提取和精准辨识,在线模型重训练时间2.55s,典型故障诊断准确率99.72%。
(4)研制了系列化可编程数字泵产品,攻克了重载大排量可编程数字泵设计制造关键技术装机应用于盾构掘进机、混凝土泵车、挖掘机、起重机等工程装备,实现国产化替代。
7、第一代新能源电驱动装载机研制及产业化应用
主要完成单位:广西柳工机械股份有限公司、柳工柳州传动件有限公司、广西中源机械有限公司、重庆大学
本项目突破传统的柴油机加双变(变矩器变速箱)系统的动力传动链结构的装载机边界创新性的使用电动机作为牵引装置,应用动力电池组作为动力能源,在达到零排放的同时,现或超越同级别传统装载机整机性能的新能源电驱动装载机。
突破传统的整机匹配技术,研究电驱动整机匹配技术。突破大电量高压储能及电能分配技术,研究大电量高压储能电池管理系统BMS,研究制动能量回收技术、节能液压技术。研究基于主动工况需求识别的动态功率分配控制系统。研究均流系统中多电机设备电流自适应分配控制技术,开发行走电机及液压电机控制策略。研究基于环境识别的能效自适应管理技术。突破高效节能新型驱动技术,研究电驱动动力传动技术,建立传动系统工作模型,开发电驱专用速箱。研究突破整机热管理技术,特别是锂电池热管理安全技术。建立声品质测试与评价方法通过声品质与主动降噪技术的融合,达到NH特性的提升。研究电驱动智能遥控技术,研究基于不同工况物料的自适应铲装技术。
在上述技术获得突破后开发柳工1.6T、2T、5T级系列新能源电驱动装载机。重点突破国内电驱动装载机的产业化空白,实现批量销售,开拓工程机械电驱动产业化的新领域。
本项目同时针对高原遂道工况突破高原适应性研究,以填补国家在该领域产品空白,积极响应政府号召,满足川藏铁路施工段隧道特殊工况的迫切需求。
目前拥有自主知识产权专利共52项,其中发明专利29项。获得省部级与行业级奖项共7项。近年来,公司在电控技术、负载敏感技术方面的技术攻关取得较大突破,连续两年获得广西科学技术奖二等奖:2018年公司新产品开发项目《装载机转向高压负荷敏感流量放大阀关键技术与应用》获得广西科学技术奖技术发明类二等奖,2019年公司研发项目《起重机负载敏感多路阀开发及其上车液压系统匹配应用》获得广西科学技术奖技术发明类二等奖。
8、高压大排量柱塞泵关键技术研究及产业化
主要完成单位:江苏恒立液压股份有限公司
高压大排量桂塞泵由配流盘、滑靴等组成,具备抗污能力强、噪声低、多种控制方式控制等特点,实现对国外同等产品之间的替代,打造国产高压大排量柱泵。本项目针对高压大排量柱塞泵的额定压力、噪声处理、控制方式等问题开展了相关关键技术研究:
(1)设计了新的双泵支承结构,大幅度缩短主轴向尺寸,有效节省了安装空间,提高泵的使用寿命和抗污染能力。
(2)采用了配流盘过渡区通孔和盲孔结合的形式,避免了轴向柱塞泵气穴、气蚀,降低柱塞腔压力突变,并通过对配流盘开设阻尼孔和指形槽相结合的方式,提高了配流盘的抗气蚀能力,并且采用该种配流盘可以有效降低整泵的噪声,使柱塞泵噪声<85dB。
(3)设计了电比例排量闭环控制器,通过斜盘角度传感器,实现了泵输出流量的闭环精确控制,提升了效率,降低了能耗,并根据控制方式设计相应控制器,使液压泵具有集成流量控制功率控制、压力控制、电比例闭环控制等变量控制方式。
本项目紧紧围绕我国工程机械的客观需求,充分发挥恒立液压作为中国高端液压泵阀行业的龙头企业的优势,以实现高压大排量柱塞泵国产化为目标,提升核心液压件的研发能力和技术水平,解决核心零部件主要依赖进口的局面。本项目成果整体技术指标达到国际同类产品水平,处于国内领先。产品已在三一、徐工、柳工等厂家的旋挖钻机上批量配套,实现对国外产品的进口替代。近三年实现了5852套产品销售,销售收入14821万元,新增利税5324万元。
9、千吨级履带起重机关键技术及应用
主要完成单位:浙江三一装备有限公司,湖州师范学院
我国大吨位履带起重机长期存在系统分析精度低、侧向承载稳定性差、机构协同控制效案低等技术瓶颈,无法满足大型核电、石化、风电场等工程场景的施工需求。本项目在国家86计划支持下,经9年持续攻关,在集成系统设计、机构协同、臂架结构三大方向取得了关键性进展,形成了千吨级履带起重机系列产品,成功实现国产化替代。项目获发明专利9件、软著3 件、发表论文6篇、参与国标1项、牵头制定团标1项。主要技术内容如下:
(1)基于大型履带起重机整体仿真设计:自主集成开发了千吨级履带起重机总体设计软件设计电子载荷表计算系统、臂架专用仿真程序、履带板自动缠绕建模仿真系统及数字孪生仿真系统,解决臂架系统非线性精确分析及超级回转装置回转支承和环轨力的精确计算问题,精度>94%,开发国内唯一接地比压实时监控、评估系统,高效评估地基承载能力,实现空载接地比压0.24MPa,较竞品提升22.5%,提高本项目整体系统的分析精度,分析精度>95%,避免核电、石化等重大工程的安全事故。
(2)基于大型履带起重机高稳定性关键结构设计:首创的高强度高刚度臂架系统可根据需要高效组合成预设宽度的变径平行臂架,侧向承载稳定性提升2.5倍,最大额定起重量突破4500吨;国内首创内回转支承加外环轨的超级回转支承系统,避免在内外部安装检测装置时机械产生滑动产生误差累计,回转速度为0.024rpm,较国际同类产品提升96%。
(3)基于大型履带起重机多机构协同控制系统设计:首次开发了多动力多机构系统协同控制技术,国际先进的双发驱动闭式液压系统,避免吊钩无法自由落钩:国内首创的千吨级起重机智能控制系统,通过力矩限制器免空钩标定算法,解决双驱行走、多卷扬、双发动机协同、超起小车与主机同步回转与行走、多卷扬穿绳效率的问题,防止系统失控导致钢丝绳损坏的问题实现变幅卷扬绳速110m/min,较同类产品提升10m/min。
项目成功应用在核电、石化等关系国计民生的重点工程中,如:CAP1400国核示范、山东鲁清石化、印度Gujarat风电场等项目,近五年新增产值74.3亿,新增利税24.4亿,创收外汇15.6亿。项目获得“明星产品、国之重器奖”、中国工程机械TOP50“技术创新金奖”、浙江省首台套等荣誉,在中国人民政府网、人民日报等各大媒体中被誉为“全球第一吊”。经浙江省工业新产品验收组鉴定,本项目己达到国际先进水平。
10、高速高压气动液压核心基础零部件关键技术及应用
主要完成单位:同济大学、上海振中建机科技有限公司、浙江永安工程机械有限公司
高速、高精度、超高压气动液压技术源于航空航天、用于工程机械、氢能源汽车及重大装备。核心基础零部件(元器件)是国家“制造强国战略”“工业强基”的重点突破瓶颈之一。气体非线性、气体压缩与释放过程的非对称性、超高压气体分子间作用力等是世界性的基础难题。在国家科技计划和国家自然科学基金等连续资助下,经过近二十年潜心研究和原始创新,在高速高精度气动液压控制方法与元件、重大装备瓶颈技术方面取得突破性进展。主要技术发明为:
(1)针对多年来困扰气动系统的低速和非线性问题,发明了高速高精度气动控制方法,进步发明了一种带套管钻的大直径气动潜孔锤,首次提出并实现了双通道潜孔锤,所研制的双通道回转接头可同时注浆注气,形成了螺旋排渣贯通式大直径气动潜孔锤设计方法。
(2)针对超高压气动控制阀及其系统的国际性难题,提出了70MPa和35MPa超高压分级压力控制方法,发明了高压气动减压阀、动静态补偿与非对称控制方法,自主研发了达到和超过国外同类产品水平的先进适用的车载超高压控制阀,实现极端低温(-40℃)和极端高温(+60℃)下输氢、加氢过程的快速充放以及行驶过程的超高压稳定控制。
(3)发明了利用加速度技术的气动液压复合打桩锤系统,通过压缩气体和锤体惯性质量的综合作用,实现锤体加速度2g以上的高速打桩。发明了可调偏心振动锤、新型气液联动复合液压缸、水下打桩用大型分体式替打,提出了基于氮气及蓄能器的打击能量调节方法。
该系列成果获授权发明专利48项,编制国家标准2项、行业标准4项,出版中文专著1部、英文专著1部,获优秀科技图书一等奖。发明成果气动潜孔锤应用于复杂地层桩基施工。发明成果超高压气动控制阀用于氢能源汽车示范应用。发明成果气动液压锤用于深海风电基础平台等国家重大工程任务。近五年累计产值16.82亿元。项目成果社会、经济效益显著。
敬请关注 《工程机械与维修》&《今日工程机械》 官方微信
更多精彩内容,请关注《工程机械与维修》与《今日工程机械》官方微信